Concluding our three-part biosecurity series, we explore the practical steps one producer has taken to prevent disease from entering and spreading through his unit, or to other holdings, proportionate to the risks he faces
Based near Shotley, just outside Ipswich, Richard Carless is an outdoor producer and believes that his location offers him an advantage in terms of the external risks his unit is exposed to. However, he still implements a strict biosecurity strategy and prioritises it as a very important factor to the overall success of his business.
“We’re lucky here in the fact that we aren’t in a pig dense region,” he says. “There’s also a relatively strong south easterly prevailing wind which helps restrict any diseases from being blown up the coast from Essex.”
But, he reinforces that there’s still no room for complacency.
“Being an outdoor unit presents its challenges and that’s why we’ve got a robust biosecurity strategy in place,” he adds.
The first protocols begin at the farm gate.
“We’ve got one of the AHDB Pork no-entry signs at the entrance and anyone wanting to enter the site has to call myself to gain permission,” he explains. “It’s useful for monitoring the flow of vehicles and personnel on and off the unit.
“This procedure is coupled with entry foot dips and larger containers of disinfectant to ensure that all visitors wash their footwear, as well as vehicle tyres, before entering and leaving.”
He adds that further enforcements are installed at the site’s entry, including a designated turning area to minimise any potential cross contamination.
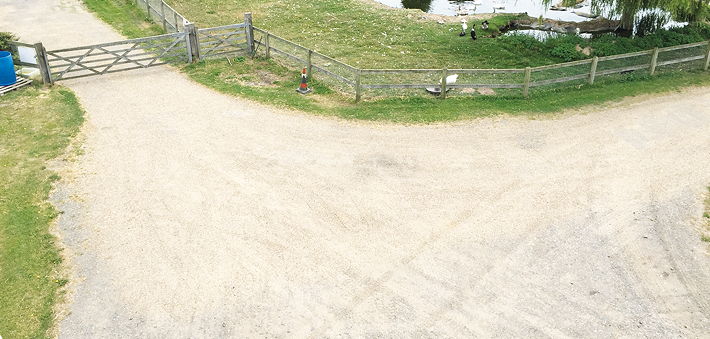
“Any vehicles entering the unit are not allowed past the turning point, including feed and transport lorries. And in turn, we ensure that none of our own machinery crosses this point, thus reducing the risk of cross contamination.”
Once within the unit, the protocols continue.
“We run a weekly farrowing system that enables us to keep on top of disease management and cleaning and disinfecting (C&D),” Mr Carless says.
“For one week in every cycle, the sows are brought indoors into a dedicated unit for servicing and artificial insemination (AI). We’re a closed unit and breed all our own replacements, bringing in new genetics through AI. This means that we have no live pigs coming onto the farm, and I think that helps reduce the risk of disease.
“After seven days the sows return to the fields and are housed in group dry sow huts. After 16 weeks they move into individual farrowing huts where they stay for five weeks until the piglets are ready to be weaned and sold, usually at about four weeks of age, weighing 8kg.
“Several years ago we were keeping the piglets up until 10 weeks of age, but we were seeing more diseases spread in the sows – this was obviously a huge concern.
“However, now that the piglets are leaving the site at four weeks of age, the issues seen previously seem to have stopped, which is great news from a biosecurity and disease management perspective,” he adds.
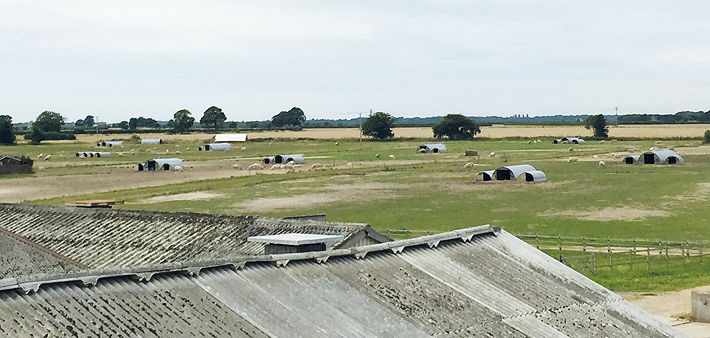
Mr Carless implements a strict C&D programme for all the farrowing huts once they become empty and before the next batch moves in.
“Once the weaned piglets are sold and leave the farm, we scrape all the huts clean. They’re then tipped on their ends and are thoroughly disinfected using a fogging machine. The machine gets into all the little nooks and crannies that a nap sack sprayer might not be able to.
“This process is relatively time consuming in comparison to some of our other protocols, but it’s probably one of the most important things we do as part of our strategy. That’s why we ensure it’s a routine procedure that’s adhered to no matter how busy we are.”
AHDB Pork’s technical veterinary team manager, Martin Smith, says Mr Carless’ strict all-in and all-out system, with thorough cleaning and disinfecting between batches, is good practice and he encourages more producers to manage their units in this way wherever possible.
“Many disease outbreaks can be linked back to the transfer of pre-existing pathogens. For this reason, good biosecurity management to minimise any co-infections is important,” he says. “What Richard’s doing isn’t anything new, but it’s certainly something that all units should be looking to implement to eradicate the spread of diseases,” he adds.
“The key is that, whatever biosecurity measures producers consider, they look at the particular risks posed for their unit or units. For example, Madec et al (1999, 2000) proposed a wider 20-point plan to control Porcine circovirus associated disease (PCVAD), more commonly known as Post-weaning multisystemic wasting syndrome (PMWS), when there was a serious outbreak in America in the late 1990s.
“I’d say this plan is a ‘gold standard’ but, in reality, its full implementation could be difficult to achieve on all units.”
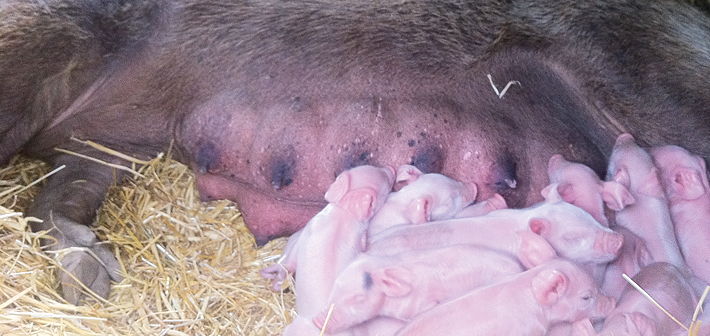
The plan is broken down into key points that apply specifically to farrowing units, post-weaning facilities and grower finisher units and highlights the importance of cleaning and disinfecting between batches in all systems. Other points include separation of pens by solid partitions, temperature control and no mixing of batches.
Mr Smith says he would encourage all producers to consider the type of points raised in the Madec et al 20-point plan as part of their own strategies, putting the standards into practice wherever appropriate, based on individual systems and available resources.
Mr Carless concurs and adds that, despite his favourable location in terms of disease pressure, biosecurity is and will remain high on the agenda for his unit.
“What we do on our unit is specifically tailored to the risks we face and that’s why we focus mainly on internal biosecurity,” he says. “I appreciate that other units may face greater risks than we do, and for this reason, their biosecurity strategy is likely to be very different to ours, but as long as it’s specific and targeted that’s what really matters.”
For more on health and biosecurity there are a number of AHDB Pork factsheets available at: http://pork.ahdb.org.uk/pig-production/biosecurity/
Part one of this series can be found by CLICKING HERE
And part two can be accessed by CLICKING HERE