Ian Smith has been Patrick Dean’s unit manager at The Old Rocket Site, just south of Lincoln, for 18 years.
He has seen many changes in that time, and has been instrumental in lots of them.
Over the years, the herd has grown to 580 JSR 90 sows, with a replacement rate of 55%. This has seen new buildings erected and, as the herd outgrew them, they have been replaced with more up-to-date ideas.
Getting rid of old concrete-floored farrowing pens that needed scraping out every day was one particularly big bonus; as we all know, staff can be better employed than using barrows and shovels. They now have time to use their stockman skills.
Ian is very proud of his four staff. They work enthusiastically, and readily take on board modern technology. It’s a true team effort, and they all work well together.
About 10 years ago I visited Ian to see some of the first rise and fall farrowing crates to be installed here. Two traditional buildings had each been fitted with 24 of the new crates, and over the course of a year, Ian compared the results with the remaining old crates. He found that the reduction in crushed piglets was sufficient to produce an extra 22t of pig meat annually between the two rooms – and that was when they were killing them at about 72kg deadweight.
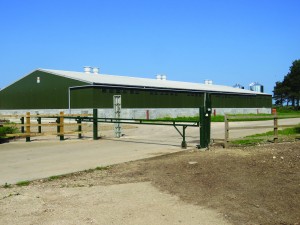
All the farrowing accommodation now features rise-and-fall crates, including the latest model from Nooyens, which is supplied by Quality Equipment. These are already proving even more effective at keeping piglets alive, with only about 0.5% of the pigs born alive being crushed, and mortality to weaning running at 6% at the most. With these sort of results, it’s easy to justify the outlay.
This, in conjunction with the farm’s latest investment in new weaner and finisher accommodation to hold the extra pigs, and plans to take the finishers from 85kg deadweight to up to 87kg, should mean the unit can attain the highest number of kilograms up the ramp at the most economical cost.
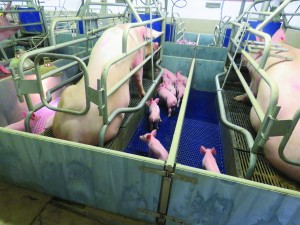
-and-fall crates
Superb buildings
The decision to add the new accommodation was made when Ian realised that some of the original older finisher housing wasn’t up to the high standards they expected, and the team was having to make three moves from weaning to finisher. Paul Wright from Checkmate was called in to advise, and the result was two superb new buildings from AM Warkup. The first is for weaners and has five rooms with two pens each either side of a central passage. The pigs are separated by eye at weaning into large and small, and each room takes one week’s supply, about 330 pigs, and the pigs stay there for 10 weeks before moving to the new finisher section at 45kg.
The unit is still on weekly farrowing, so everything fits perfectly and they have had no need to expand the farrowing areas. While suckling, the piglets have access to a Rotecna round trough for creep feed, and when they go into the new weaner housing, larger versions of those troughs are put in for a few days, which the pigs take to immediately. They are removed when the piglets get used to the Crystal Springs feeders.
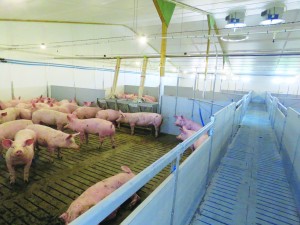
The new Warkup finisher building, meanwhile, has three rooms, each with eight pens, that take one week’s worth of pigs – there’s also some 10-year-old finisher accommodation on the unit which is still working well and takes the rest of the pigs. Through investment in genetic, nutritional, health and management improvements, numbers produced have increased considerably to 28/29 pigs per sow per year, and the intention is to build another finisher unit to handle the extra production.
Skov ventilation is being used in the new buildings and this seems to be working well. And it’s anticipated that the growth of the stock, produced from the JSR GC900 boar, will see the finishers reaching 115kg liveweight at about 22/23 weeks.
Slurry separator
A dry slurry pump – which was quite expensive to put in, but was installed to also accommodate the third new building when it comes – carries the slurry from the new buildings about quarter of a mile to a separator; the liquid portion goes to a slurry store.
A tank at the side of the farm’s loading ramp captures wash-down water after loading, and this is emptied when necessary and taken by tanker to the slurry store.
Nutritional advice for pigs larger than 12kg comes from Harbro, which actually mills rations for the unit on one of Patrick Dean’s arable farms, and the feed is brought in by trailer. The creep and sow rations are supplied by ForFarmers.
Another thing the unit has had to do, to satisfy the local water company, is to install a water pump. This boosts the mains supply, but more importantly helps avoid any backflow from medication in the farm’s water tanks.
As you approach the unit, you’re faced with a security gate, and as feed lorries or livestock lorries arrive, the vehicles are disinfected on entry. I am seeing more and more of this sort of thing, and wonder when it will be on every pig farm.