Most farmers know the cost of their feed, the feed conversion figures and growth rates of their pigs and days to slaughter. But do they know the costs of running their finishing houses?
According to Tim Miller, ARM Buildings’ environmental specialist, many do not. He has come up with some surprising figures and suggested ways to reduce energy costs without sacrificing performance.
“Energy prices are becoming more of an issue, especially with the increasingly popular B&B arrangements,” Mr Miller said.
“Farmers providing finishing houses on contract are paid a set amount per pig place, which includes housing, labour and electricity. Electricity costs have often been overlooked but, with the spike in prices, they have become significant, especially during recent hot summers. Some farmers say they have been losing money as a result.”
Finishing house costs
So, what does it cost to run a finishing house? A typical installation today involves 2,000 pigs, either housed in two, 1,000-place or four, 500-place buildings. Above this number farmers need an environmental permit.
The price farmers pay for power varies but, today, a typical charge is 22p per kWh, with some users paying less, and others paying more, in Mr Miller’s experience.
Barn ReportPro monitoring has shown that fans on a standard 2,000-pig unit consume 22-24kWh per pig place for ventilation, lighting, running feed lines and pressure-washing, for example, giving a total cost of £9,686-£10,560.
The fans consume the major share – around 75%, which varies according to the season. In summer, consumption per pig can be as much as 6-7 kWh, but in winter it may drop to as low as 2.25 kWh per pig place, with spring and autumn in the middle at around 4 kWh, depending on the weather.
“These figures have shocked some farmers who haven’t included them in their calculations when agreeing their B&B contracts,” said Mr Miller.
However, with traditional set-ups there are ways of making substantial savings through efficient fan use, he pointed out.
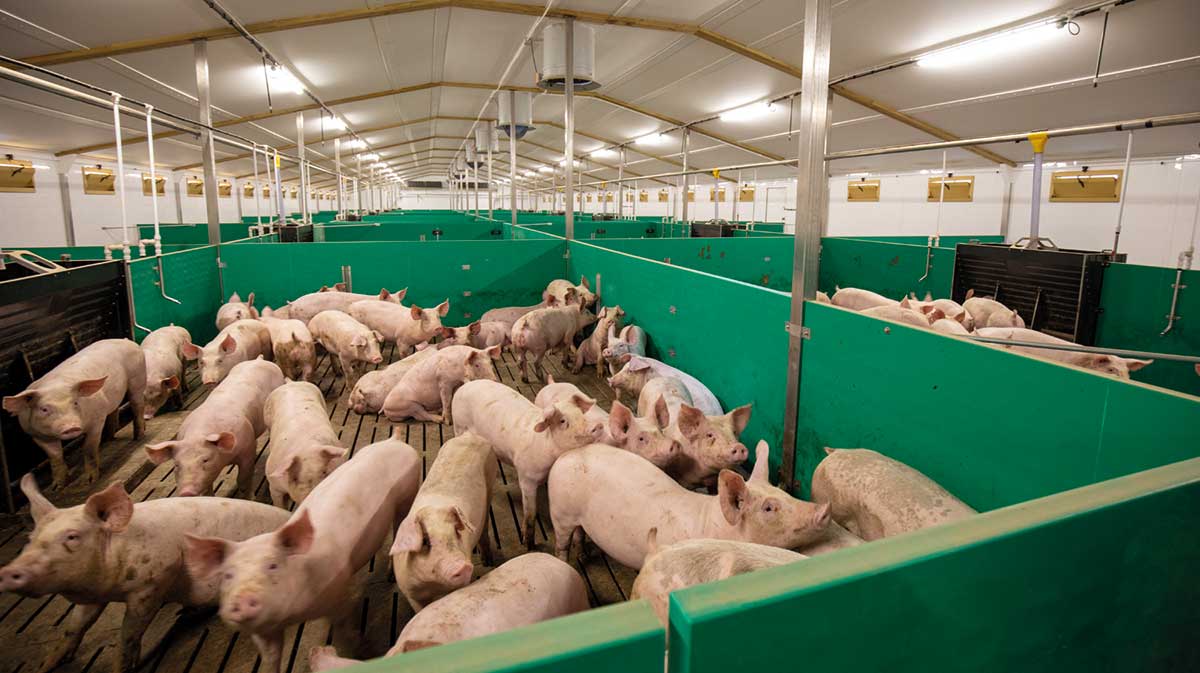
Controlling fan use
The principal approach is staged fan control. This involves turning individual fans off, and running others at full speed to achieve the same ventilation rate, rather than all fans running at a lower speed. This conserves large amounts of energy and can save 8kWh per pig place, up to £3,500 annually.
If not supplied from new, programmes can be installed retrospectively to achieve this. The Farmex Dicam system, supplied with ARM’s buildings, for instance, can rotate the use of fans to equalise wear and tear on the motors, rather than leaving a fan idle all winter until needed for summer ventilation.
Along with more efficient fan use, there are programmes to vary ventilation rates depending on the time of year.
In summer, there can be an external temperature ‘trigger’, which causes the inlets to open to a greater extent than normal to form a sort of hybrid ACNV (automatically controlled natural ventilation) system, which can give further savings.
Conversely, a winter programme with an external trigger point of, say, 5 deg C, gives tighter inlet settings to conserve warmth.
Typically, such programmes can be installed at less than half the value of the savings, giving a substantial payback within the first 12 months, according to Mr Miller.
While little can be done to save energy for feed distribution or cleaning, lighting is another smaller, though significant, consideration. Again, programmes can be installed to ensure light is only provided where and when needed and at the intensity levels required. “This is something which is often overlooked,” he added.