As the winner of the brand-new Sustainable Farming award at last year’s National Pig Awards, Lincolnshire Pork Co was described as a true champion in this field.
The inspiring vision and commitment of the Ward family is having a far-reaching positive impact across the business – on its pigs and employees, as well as the natural environment.
Meryl and her son, Sam, are developing a circular farming system, integrating their indoor pig enterprise with the business’ 900ha arable operation and their farm shop, Uncle Henry’s – while generating green energy and cutting emissions.
They run two 750-sow breeding units, rearing pigs to 35kg before moving them to deep-straw finishing units, some of which they own, alongside some contracted bed-and-breakfast units.
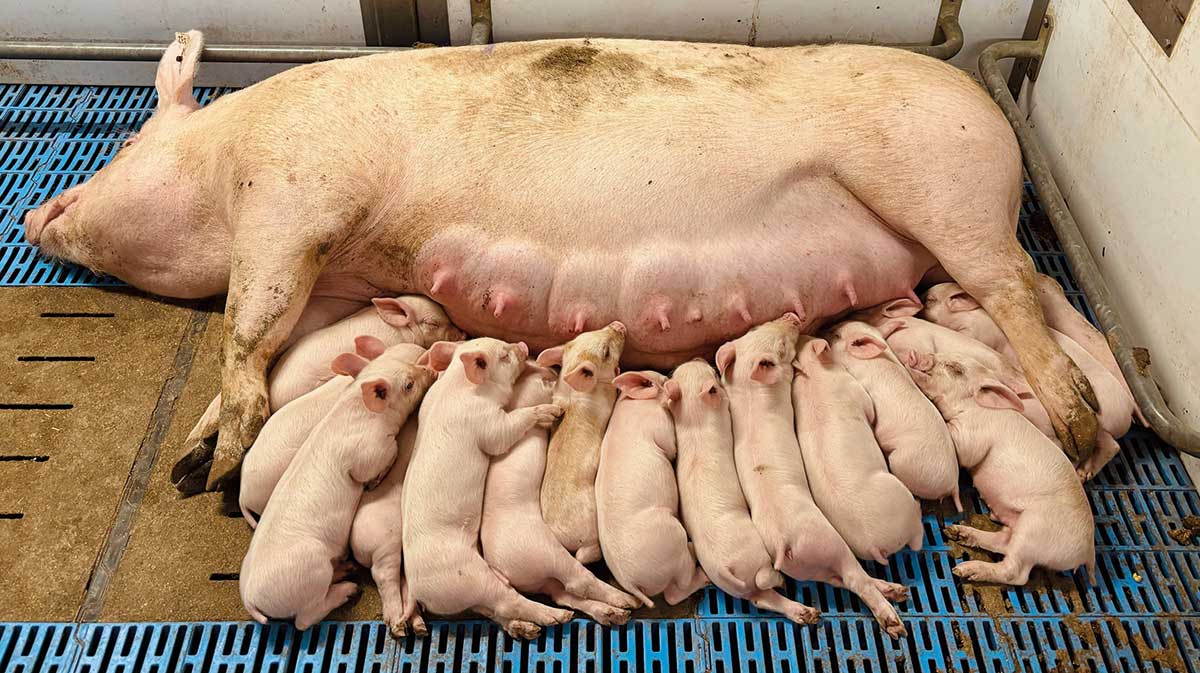
Renewable energy
The business is 155% self-sufficient in electricity, with anaerobic digestion, wind and solar energy providing heat and power for the pig buildings, farm shop and butchery, plus electric vehicle (EV) charging.
Greater energy security was a major motivator for investing in renewable technologies. “With an indoor herd, energy is our second-biggest cost after pig feed,” said Sam. “Producing our own renewable energy protects us from energy price hikes and helps make the business more resilient.”
Their first step, in 2010, was a feasibility study on all options for renewable energy generation and there are now two wind turbines generating 100kWh each, solar panels with a capacity of 90kWh and two 125kWh anaerobic digestion plants.
So far, they have three EV charging points. There are two for staff vehicles and the farm vans (the lighter transport fleet), one on the arable unit and the other for the farm shop and office buildings.
“The third is for Uncle Henry’s customers, which is currently being used for three to four charges per day, which is building up nicely as more people hear about it,” said Sam. There are now plans to put in a fourth charging point at the pig unit for the herd manager.
Renewable energy is at the heart of the circular system Lincolnshire Pork Co has developed for its arable and pig production enterprises. “We’re not only producing electricity and heat, but also digestate of a consistent quality to fertilise crops,” said Meryl. “We’re capturing ammonia and, in turn, the anaerobic digester is using homegrown maize and sugar beet pulp, along with the pig muck.”
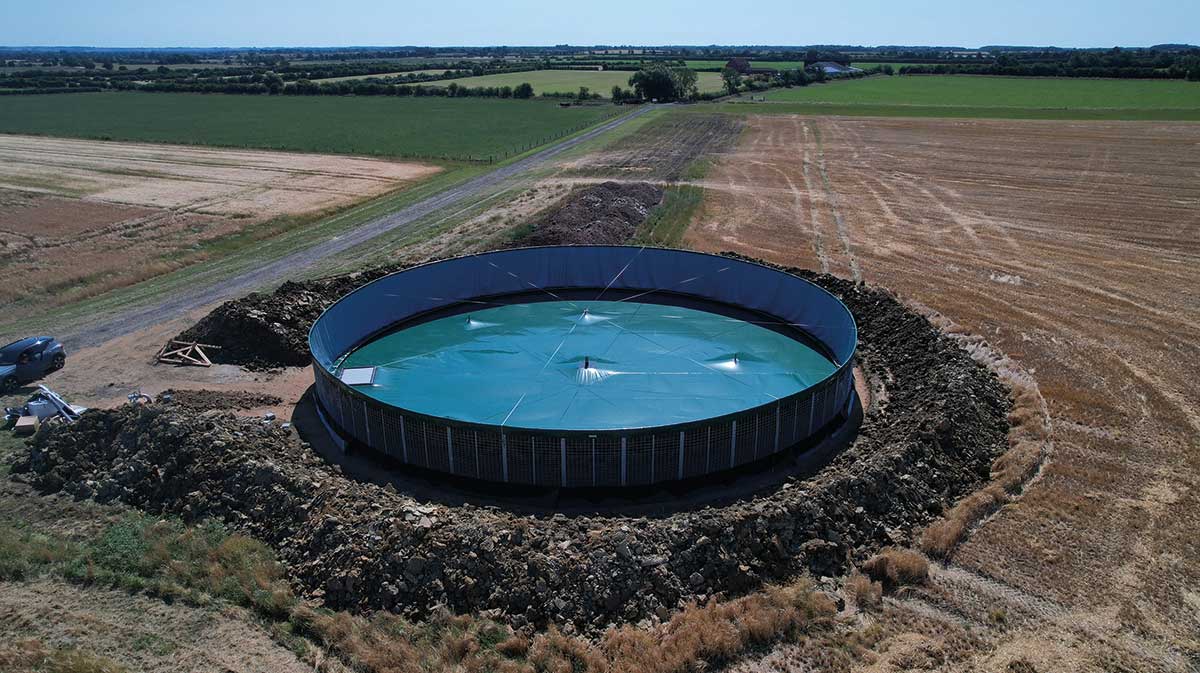
Pig building investment
In 2019, the Wards began a major reinvestment project to replace outdated buildings on the breeding units. They built new fully-slatted farrowing and nursery accommodation, incorporating a slurry flushing and acidification system and adaptable farrowing pens, which provide the option of non-confinement of sows.
The new modern buildings have significantly helped with health, welfare and production efficiency. Higher ceilings help ensure good air distribution and a high-pressure misting system helps manage the temperature during hot weather.
Pig management and the flow of pigs around the farm are now much more efficient, with each department all in one room. There are now more pigs leaving the site than with the old system, but with the same number of sows.
“Our numbers born alive are still steadily increasing, but we’re not specifically targeting that,” said Meryl. “The team’s main aims are to have even litters at birth, good-sized piglets and low pre-weaning mortality.”
Having a more efficient, modern system has also enabled further improvements to working arrangements for staff, including working hours and weekend rotas, while keeping to the same number of employees.
The herd is now closed to live breeding stock replacements, after working through an issue with porcine reproductive and respiratory syndrome (PRRS) a couple of years ago, and pig health has stabilised. The team is currently focused on making lots of small tweaks to improve performance.
For example, they are able to continually trial the impact of feed, using a platform weigher in the corridor of the new nursery accommodation to record the weight of each pen of 40 pigs. “Every batch is weighed when the weaned pigs go in, then at 15 days, 29 days and 42 days,” Meryl said.
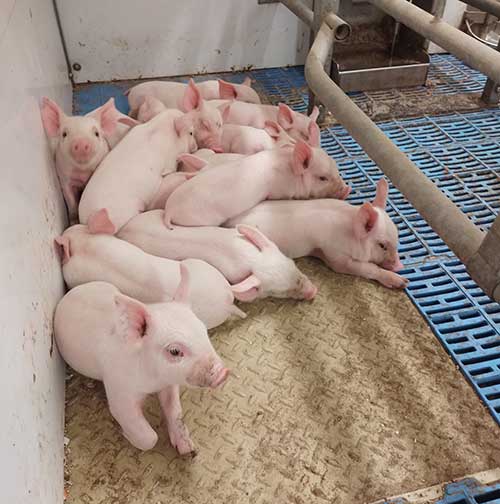
Slurry management and infrastructure
The slurry flushing and acidification system under the slats has significantly improved the environment for both the pigs and people working in the farrowing and nursery buildings. Because it’s flushing continuously, there is no slurry crust build-up under the slats, reducing flies and dust.
Air quality has also improved outside the building, while the shallow slurry pits future-proof the system from an emissions point of view and for extended producer responsibility (EPR) compliance.
“We wouldn’t be without it now,” said Meryl. “There are the ongoing running costs of electricity for the pumps, as well as the initial investment to pay back, but we just have to factor them in and we’re seeing the benefits. It’s a modern way of pig farming.”
Acidification also increases the ammonium in the slurry, which is not as volatised as ammonia, and it helps make the nutrients in both the slurry and soil more available to crops.
Since completing the pig unit rebuild a couple of years ago, the business has continued to invest in infrastructure, carrying out extensive remedial drainage work and covering the slurry stores with a rigid fixed cover.
Umbilical slurry pipes and satellite storage tanks have also been installed on neighbouring arable farms. This has provided 10 months’ worth of storage, allowing slurry to be spread at a time that best suits crop nutrient requirements.
“We started readjusting how we used the nutrient resource in slurry when the Ukraine war caused the huge increase in fertiliser prices, refining it as far as possible and buying in as little bagged fertiliser as we could,” Meryl said. “It’s still ‘work in progress’ and involves putting in place straightforward heads of terms agreements with neighbours for the tanks on their farms.”
The Wards do not purchase any phosphorus (P) and potassium (K), but buy in a proportion of their nitrogen and sulphur requirements.
“For example, we buy in bagged fertiliser for cereal crops, which have a total requirement of 200kg of nitrogen per hectare, as they will only get 120kg of that from the single pig slurry application we can make,” Sam said.
The new infrastructure has extended the slurry spreading season and is paying dividends in light of the extreme volumes of rain seen in recent years.
“Instead of autumn spreading, we transport slurry to the satellite tanks over the winter and spread it in the spring,” Sam explained.
“We aim to put the tanks in locations where we can pipe the slurry to them overground and the umbilical system reaches most of the farms so we can shift big volumes very quickly.”
These investments have helped to keep clean and dirty water separate and enabled slurry to be moved around in the most cost-effective manner.
“We cannot afford to be capturing excess rainwater and moving it about,” said Meryl. “We’re saving a lot of labour and diesel, while making slurry a highly useful resource.”
The main challenge is the enormous expense of the umbilical pipes and storage tanks, so government grants have been very welcome for the business.
“The government needs to keep offering grant funding year on year. Things wear out or need maintaining and circumstances change – there might be producers in a better financial position than a couple of years ago, who are now able to find the match-funding,” Sam said.
Homegrown feed
Homegrown barley, wheat and, more recently, rye have always been used in pig feed rations, with the aim being as self-sufficient in feed as possible.
Rye has been part of the arable rotation for the past four years and is included in finisher diets at about 20%, which is based on the amount available.
It acts as a replacement for wheat, with comparable pig performance, and it is generally a more sustainable crop to grow, with half the nitrogen requirements of wheat. Rye also produces more straw.
“Partnering with ABN, we also have access to co-products such as wheat feed from the flour industry, which, again, increases the sustainability of our feed,” said Sam.
The proposed one-year delay to the EU Deforestation Regulation that would have made sourcing soya harder and more expensive is a relief, but the issue has not gone away. “We’ll potentially be able to access peas or beans as an alternative to soya in future. We already grow vining peas, but beans are not that well suited to our land,” Sam said.
Further moves towards lower-input and more sustainable practices on the arable side of the business include planting cover crops and companion cropping.
They have also established a 10m controlled traffic farming system where they are growing second cereals, to help limit compaction and reduce the amount of cultivation needed.
The pig enterprise operates a muck-for-straw agreement with Lincolnshire Pork Co’s arable enterprise, as well as with neighbouring arable farms.
“We’ve recently joined the AHDB baselining project with John Gilliland,” added Sam. “It will be an interesting process to try to get everything measured in a useful way, including soil health, carbon calculations and biodiversity benefits.”
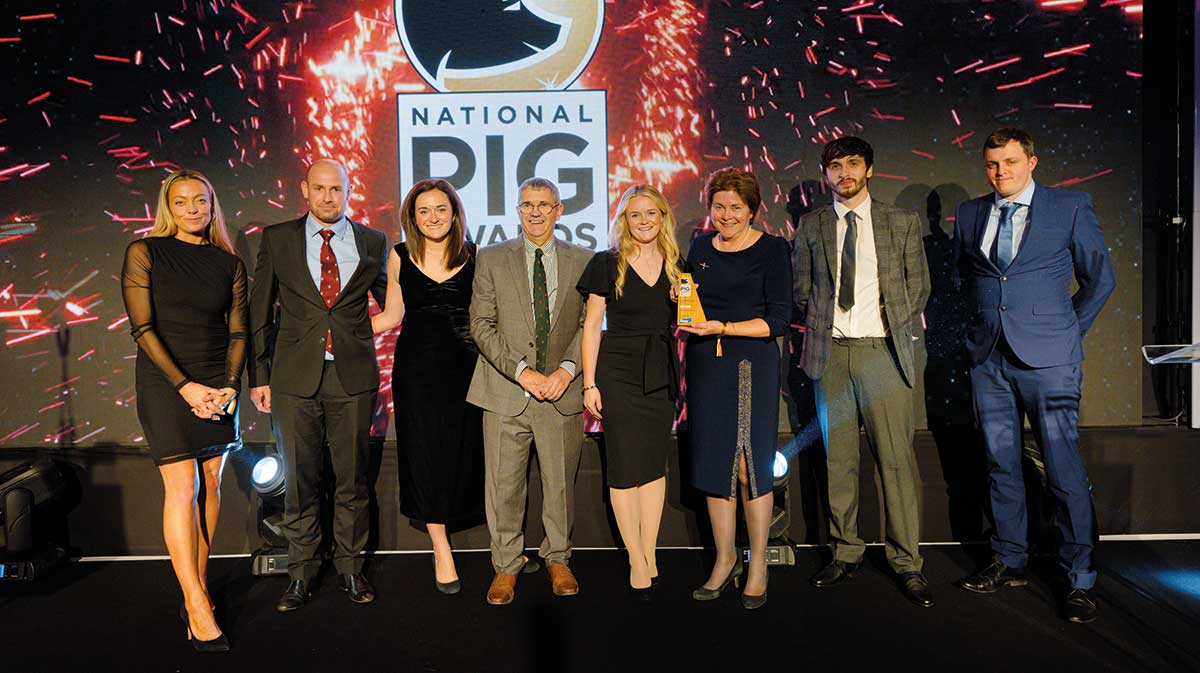
Looking ahead
It is important to Lincolnshire Pork Co to keep building its reputation as a brand that values sustainability.
“We spend a lot of time on social media explaining what we do to our customers, although we don’t know how that translates into sales at Uncle Henry’s,” said Meryl.
“We also supply Co-op stores with added-value pork products, and it is very keen to promote the sustainability of farmer suppliers to its membership.”
More broadly, the 2040 target for UK agriculture to reach net zero, along with banks announcing they will use green credentials for future lending, mean every farm business needs to be reducing its environmental impact. “We can’t actually afford not to,” Sam said.
The business is now in a consolidation phase, with the focus on paying back the capital cost of the investments made and maximising their benefits.
Putting in renewable energy infrastructure and transitioning the farm’s light transport to electric vehicles were relatively ‘low-hanging fruit’ that the Wards felt confident to go ahead with.
“There are a couple of much bigger things for the future that we’ll wait for government and industry to provide a clear direction on, like soya sourcing and whether heavier transport, such as our lorries, should move to electric or hydrogen fuel,” Sam said.
The new pig buildings were a massive step, but they have provided numerous efficiencies, including good pig flow and economies of scale.
“The challenge is paying for them,” said Meryl. “Like many producers, we just haven’t had high enough pig prices in the industry to reinvest, so we’ve often carried on with financial margins. Cost-of-production contracts need to take this into account. Anything is doable, if producers have confidence in consistent returns.”