Denmark, a comparatively small country with just five million inhabitants, produces enough food for a population of 15 million. More than 29 million pigs are reared on 3,800 pig farms, and 90% of the pork produced in the country is exported to in excess of 140 different countries. Anders Leegaard Riis of the country’s SEGES Pig Research Centre says that the Danish co-operative model has been recognised as the foundation of the long-term success of Danish agriculture.
“The first pig farmers’ co-operative was established in 1887 and it quickly became the industry standard, where pig farmers are stakeholders in both the production and processing of meat from their animals,” he explains.
“About 90% of pigs finished in Denmark still go to market via the co-operative system, and the vast majority of farmers here deliver pigs to their local co-operative slaughterhouse on a weekly basis.”
Mr Leegaard Riis says that, for pig farmers, being a member of a co-operative extends their interest beyond the farm gate, and the transparency inherent to the system allows trust to develop between the primary producer and processor or retailer.
“The co-operative ethos in Denmark has also encouraged common funding of world-class research and development to make sure that the country’s pig farmers remain at the leading edge of global competition,” he adds. “The SEGES Pig Research Centre co-ordinates a wide range of producer-funded research projects with an annual budget of £11 million. Much of the research takes place in the field, and SEGES currently has about 200 farms engaged in trials. The testing of new environmental technologies forms a significant part of this work.”
Denmark’s livestock producers are facing increased pressures to limit the environmental impact of their production.
“The Danish pig industry has already been subject to some of the strictest environmental legislation in Europe,” Mr Leegaard Riis says. “These rules have included fixed limits on the number of animals that may be kept in relation to the land available for the spreading of manures, as well as detailed rules on its storage and application to fields.
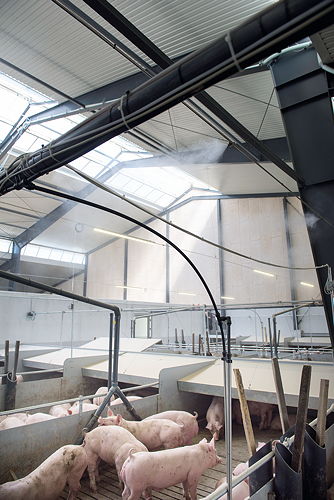
“Because of this, it’s no surprise that our organisation attaches great importance to helping our farmer members meet the environmental challenges of today and the future. And, with regards to emissions from animal housing, current environmental regulations cover three parameters.
General requirements
“First, there are some general requirements for ammonia reduction and Best Available Technique (BAT) emission limit values. The general requirements for ammonia reduction are 30% for finishing pigs and sows, and 20% for weaning piglets in relation to a reference level of emission (Standard numbers 2011).
“The requirements cover both new facilities and those being refurbished. For new facilities, the farm must use BAT technologies, where the total level of emissions must meet the limit values, which can be achieved by use of BAT ammonia reducing techniques.
“Second, there are rules affecting ammonia deposition rates in ‘sensitive’ rural areas. Maximum rate of deposition depends on the distance from the facility to the area and three categories of sensitive area are defined in the regulations: Natura 2000 area (maximum 0.2, 0.4 and 0.7kg N/ha); High moor or heathland of more than 10ha and open grazing land more than 2.5ha (maximum 1kg N/ha) and other ammonia sensitive areas (maximum 1kg N/ha for new facilities).
“Third, there are requirements relating to odour concentration to neighbouring areas. Again, three categories are identified in the regulations: Urban zone (maximum concentration 5 OUE/cubic metre); Estate or group of more than seven dwellings in a diameter of 200m (7 OUE/cubic metre); and a single dwelling (15 OUE/cubic metre).
Environmental technologies
Mr Leegaard Riis highlights that, over the years, the Danish government has made different forms of grant available for investment in environmental technology, based on financial support from the EU and the Rural Development Programme.
“The Environmental Protection Agency publishes a list of environmental technologies (see: http://goo.gl/Z3xB8K), that have been tested and documented to be environmentally efficient and operationally stable,” he says. “The list includes technologies that can reduce ammonia and odour emissions from livestock units.
“With regards to investment costs and benefits of these new technologies, it’s difficult to give a simple answer as the impact will vary according to the system introduced and the type of production involved. In the case of pigs, different results will be obtained for sow, weaner or finisher production. To be defined as a BAT technology, the cost for reduction must not exceed £10/kg of reduced nitrogen.
“It’s our experience that, while many investments in environmental technologies represent an extra cost, they can often provide an opportunity to expand and develop pig production systems.
“Danish pig farmers can document significant improvements in achieving more sustainable production. They produce a kg of pork today with approximately half the environmental impact as that of 1985. Danish farmers have taken a lead in the application of new eco-efficient technologies to reduce the environmental impact of modern pig production.”
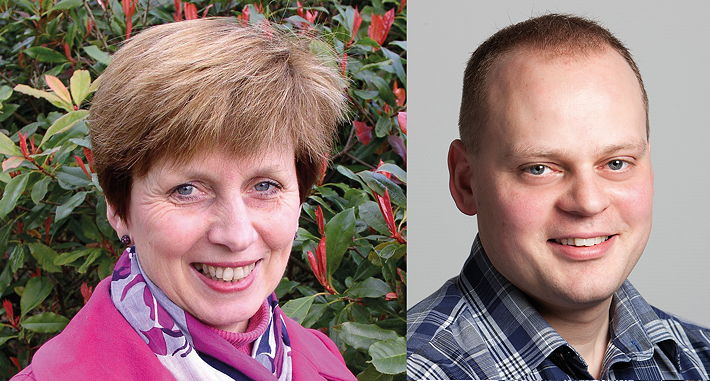
AHDB Pork showcases the Intellifarm concept
With tighter ammonia and odour legislation set to come into force from the EU, AHDB Pork is equipping English producers with a toolbox of buildings technologies that can help them future proof their businesses.
AHDB Pork’s environment and building research coordinator, Susan Rabbich, highlights that the toolbox already includes information on pH slurry reduction systems and, further to this, she’s informing producers of the Intellifarm concept that was the highlight of the organisation’s study tour to Denmark.
“During late September, we took a group of about 20 producers and industry stakeholders to Denmark to look at how Danish farmers are reducing ammonia and odour,” she explains.
“We saw a handful of different buildings technologies while on the study tour. However, one technology that really stood out was the Intellifarm concept for use on pig units and dairy farms. This concept is based on a hybrid ventilation system which uses automatically controlled natural ventilation (ACNV) and fans to provide crossflow ventilation under the slats.
“There’s also an option for the exhaust air to then go into a scrubber to remove the ammonia, dust and odour before being expelled to the atmosphere. It’s claimed that the system can remove an average of 75% of the ammonia and 50% of the odour emissions – which can help producers to obtain their environmental permits.”
Advantages of such a ventilation system include:
- low energy requirement as only the floor suction requires energy;
- reduced emissions of ammonia, odour and dust;
- potential for reduced levels of disease and other conditions that may be caused by an unpleasant atmosphere;
- improved working conditions; and
- overall remote control of the system can be achieved through computer, tablet or smartphone.
Ms Rabbich explains that the Intellifarm concept is another option for consideration by English producers that will help to reduce ammonia and odour. However, it’s very different to the pH slurry reduction system as it focuses solely on ventilation.
To view photo stories of innovative building investments, including the pH slurry reduction system in Denmark, visit: http://pork.ahdb.org.uk/news/photo-stories/
To find out more about the study tour to Denmark, visit: http://pork.ahdb.org.uk/research-innovation/study-tours/