Dutch livestock hygiene solutions supplier MS Schippers has developed a bold new pig-housing concept for the farrowing and growing sectors that merges existing technology from the logistics industry with the best health practices in pig keeping to produce a system that appears to have huge potential for increasing performance. Pig World editor Graeme Kirk reports
MS Schippers is probably not what you’d consider a conventional company. The family-owned business, which was founded a little more than 40 years ago, actually started out by selling cigars door-to-door to farmers from its base at Bladel, near the border between The Netherlands and Belgium. A realisation that there were many other products that the company’s customers also needed resulted in the decision to sell supplies for pig production, with cattle, sheep, goat and poultry products also being added to the Schippers offering in the years that followed.
Today, the company operates worldwide with a product range that’s been developed to appeal to all professional livestock farmers – although it still clearly has a soft spot for pig production. The firm is passionate about reducing antimicrobial use and improving pig health, which is perceived a pig industry issue in much of Northern Europe, and a banner above the main entrance to the company’s headquarters – and repeated on stickers on employee’s cars – states “without antibiotics – that is our goal”.
Pig production also takes pride of place in the company’s remarkable central showroom and meeting area (a bright, airy space that features a fish pond running through its centre), where hygiene equipment and clothing in a range of colours, to distinguish them for use in the different sectors of a pig-production enterprise, make an impressive display.
This passion for producing healthy pigs without the need for antibiotics has now seen MS Schippers develop a brand new concept for pig production. The company has started with a blank sheet of paper and come up with a way of keeping pigs that’s unlike anything that’s been tried before.
European pig division manager Mart Smolders says the firm has spent many years working with pig producers to raise pigs in a healthy environment, and it has a developed a checklist that now extends to more than 200 items to try and achieve optimal biosecurity on a unit – but this is no longer enough.
“We know that farms with specific pathogen free (SPF) status or that have very high levels of hygiene get much better results, but it’s also understood that it’s very difficult to get to that point,” he adds. “The depop/repop process is very expensive, and once you have a clean herd, how do you keep it clean?
“We realised that the whole production process needed a rethink to come up with a new way to raise piglets without exposing them to the checks that exist in conventional systems. If we can achieve that, we can get closer to realising our vision of keeping healthy pigs without antibiotics.”
The starting point for the new system, that MS Schippers has called HyCare, was the realisation that about eight to 10% of all sows in a herd will be carrying disease that they’ll pass to their piglets, and unfortunately these tend to be diseases that can only be identified post-mortem.
“To put that another way, this means that about 90% of piglets are born free of disease,” Mr Smolders says, “but under traditional production methods we mix the piglets at weaning or have bad hygiene – the piglets are exposed to germs from the previous batch – so that the whole population is affected. It’s logical, therefore, to presume that if we keep the different batches of piglets separate with high hygiene, we’ll see a huge difference in production.”
It’s often said that rather than concentrating on what we’re doing right to improve pig production, we should spend some time looking at what we might be doing wrong to hold back performance, and that’s at the heart of the Schippers HyCare concept – conventional pig accommodation is not up to the job. Only by treating every litter as an individual unit can you remove the setbacks caused by bacterial disease!
Technology driven
The way that the company has incorporated this basic idea into a workable pig production concept is ground-breaking. At the heart of the system are moveable, self-contained pens that are about the same size as a conventional farrowing pen. These pens – which are made from moulded plastic with smooth walls about 75cm tall all round (with a slot-in door at the back) – are fitted with a slatted floor, a farrowing crate and heat pads.
The pens accommodate the sow from five days before farrowing until weaning, and then, once the sow has been removed, will go on to hold the piglets until they’re about 60-days old. If preferred, the piglets can be transferred to a grower pen without a farrowing crate at weaning time. Both pen types feature a sump below the slats that will hold at least a week’s production of slurry from the farrowing and growing, or growing only, phases.
The Schippers HyCare pens are moved between the different parts of the set-up on robots that have been borrowed from the logistics industry. Many new warehouses now use automated systems to store and recover pallets from multi-level shelving, and that’s very much the process that’s been adopted here.
According to MS Schippers pig adviser Gijs Kennis, the pens can be moved by the robot between five different zones within the HyCare system.
“There are two zones actually within the production system – what we call the ‘Farrowing Room’ and ‘Production Rooms’ (there are types for nursing and growing) – and three outside – the ‘Toilet’, ‘Washing Machine’ and the ‘Workplace’,” he says. “Each of these has a specific role to play.”
Starting outside the controlled environment of the system, the role of the Toilet is to clean out the sumps of the pens. This is all done automatically, and the slurry is pumped to external storage in a closed system that removes the opportunity for contamination in the production building.
The Washing Machine is also self-explanatory, as this is simply the process by which the individual pens are cleaned and disinfected ready to be reintroduced to the HyCare system with the next batch of sows.
Finally, the Workplace is where farm staff carry out routine tasks on the pigs from the Production Rooms. The Workplace at Schippers’ prototype HyCare building has “parking spaces” for two of the moveable pens with a platform on three sides to allow easy access to the sow or piglets without actually climbing inside.
This set-up allows the unit staff to work at one pen – giving vaccinations or other treatments – while the robot goes off to get the next pen that’s needed to go into the other space. The environment in the Workplace can also be adjusted to make it better suited for the unit staff, rather than the pigs, creating a more pleasant atmosphere for them to work in.
Working prototype
Inside the controlled environment building, the walls and surfaces are more like a warehouse than a conventional pig building. There’s no need for easily washed surfaces, because each moveable pen is, in effect, a self-contained pig house and it’s this that gets the full wash-down treatment between batches.
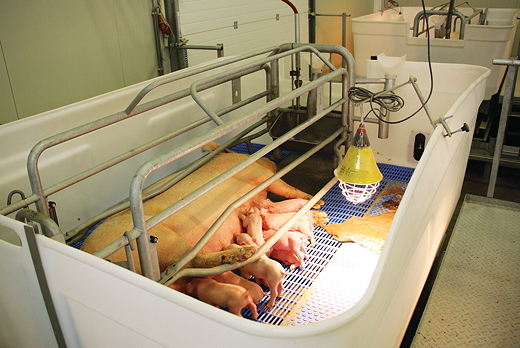
At MS Schippers working prototype of the HyCare system there’s a Farrowing Room for six sows. I suppose you could compare this to two rows of parking bays off a single-track road. The sow is loaded into a pen at one end of the house and the robot then carries the pen to one of the bays. Each bay is surrounded by a platform on three sides, and it’s from here that the farm staff can assist with the farrowing if required. This ease of access should ensure that the pigman never actually needs to enter a pen, keeping cross contamination between groups of piglets to a minimum.
The temperature in the Birth Room is kept at an ideal level for the pigs and a heat exchanger is use to ensure a high level of ventilation and air quality, there are heat lamps that can be clamped to the pen if required. Pipes to deliver feed and water to the sow are also plugged into each pen in a way that’s replicated throughout the building.
Unlike conventional farrowing accommodation, the sows remain in the Farrowing Room for no more than five days after farrowing as, after the litter has settled down, the moveable pen is collected by the robot and moved to the Nursing Room.
This is where Schipper’s concept takes another leaf from the logistics book of best practice and, as I hinted at in last month’s Pig World, has added an element of pig production that many could see as factory farming.
“It’s clear that the fact we need passages for the robot to operate in that are much wider than those you’d traditionally see in pig buildings, means that the HyCare system has the potential to use a lot more space, but we can get around this by stacking the moveable pens two high in the Nursing and Growing Rooms,” Mr Smolders says. “Again, the environment is carefully controlled, and connectors bring food and water to the sow, but we also pump in fresh air for the sow from outside as we know she enjoys a slightly lower temperature than the piglets require. And, of course, the air leaving the building can be scrubbed to reduce emissions.”
This is probably the most radical part of the system as it’s essentially a closed, controlled-environment room – as far as heat and light is concerned – with large doors for the robot to enter along a central track and place the moveable pens two high on shelves on either side. But it’s also hard to fault the logic of the system. Muck and slurry isn’t an issue because of the pens’ sumps, and many producers will tell you that pigs perform best when left to get on with it.
Monitoring systems for food and water use can highlight any problems emerging in a particular pen (as can weigh cells built into the robot that will monitor the performance of each pen as it’s moved), but the system also allows for more pro-active stockmanship.
“We can put a chair on the robot and it will carry the pigman past every pen so he can look in and make sure everything is alright,” Mr Kennis says. “It’s a feature of the HyCare system that it’s impossible for the stockman to reach into the pens in the Production Rooms. If a problem is spotted, the pen will be collected by the robot and taken to the Workplace to be sorted out.”
While it would also be possible to fit a camera systems to monitor the pigs, Schippers currently feels this would be unnecessarily expensive.
Once the sow has been removed at weaning, the pens can be moved to the other type of Production Room, the Growing Room. This follows exactly the same format as the Nursing Room, although the feed and water delivery system is set up to cater for the weaners rather than the sow.
There’s an added benefit to the HyCare system at the weaning stage and that’s the fact that the fact the piglets remain in their established group when the sow is removed. Not being mixed with other piglets reduces stress levels and leads to a smaller check in growth as they make the transition from milk to other feeds.
Positive feedback
MS Schippers introduced Dutch farmers to the concept late last year and got overwhelmingly positive feedback. From that point, the project proceeded to the prototype stage and initial trials. So far there have been seven batches of six sows put through the system, and a little more than 500 piglets delivered, and the early results have certainly been encouraging.
To test the HyCare system, the company has been splitting groups of sows on a local farm, leaving some to go through farrowing at home and putting some through the prototype unit. As the piglets all share the same genetics and get the same very basic diet, the results should show the benefit of the new system.
While it’s still early days, these trials show that the piglets born and raised in the conventional system weighed 20kg on average at 60 days (the Dutch average is circa 18kg), while those put through the HyCare system weighed an average 26kg at the same age. Schippers also notes that the test farm uses hardly any antiobiotics.
While there are still many questions to be answered – including, for example, how will the pigs react to being mixed at 60-days old when they finally go into conventional finisher accommodation – there’s no doubt this is a bold concept that’s worth a great deal of consideration. As demand for food increases in line with global population, this could be one route to ensuring pork remains a sustainable foodstuff and can compete with chicken as a protein source.
MS Schippers is confident that HyCare has a future in the pig industry and is looking for its first full-scale customer for the system. The company estimates that for a 1,000-1,500 sow herd, it can be installed for the same cost as conventional pig farrowing and grower accommodation, while for larger installations it could work out cheaper.
Inspired by the results and experiences from the HyCare project, the company has also developed the HyCare method, which it’s using to coach commercial farms in better hygiene. This is also bringing tremendous results by reducing mortality in suckling piglets and weaners, and reducing the animal health costs.
More information on the HyCare system can be found online at: www.msschippers.co.uk
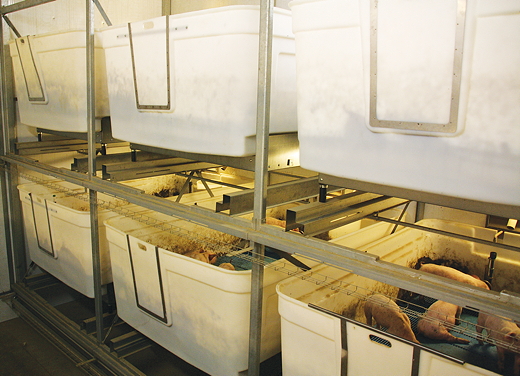